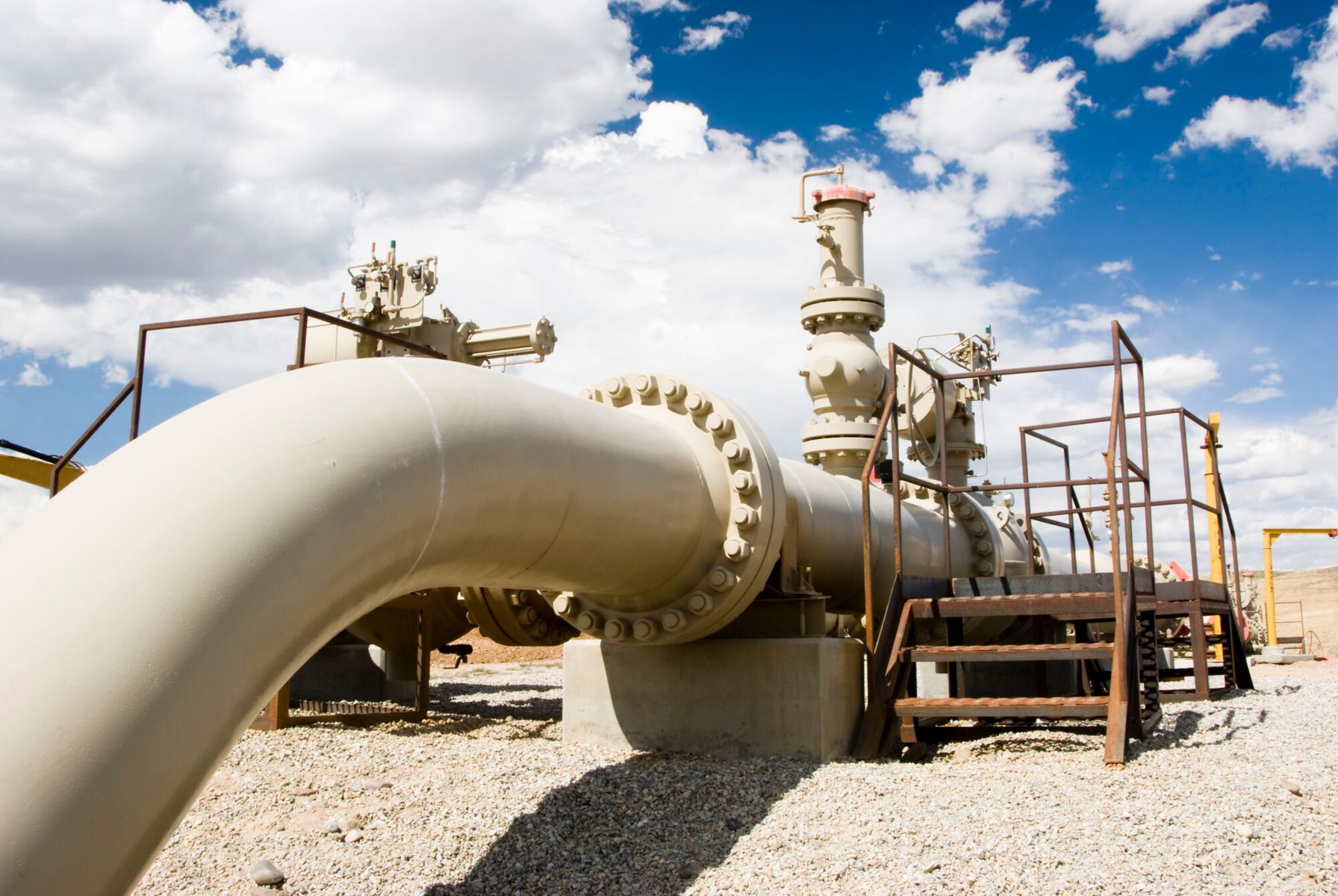
What is Pipeline Hydrostatic Testing?
Pipeline hydrostatic testing is a method used to verify the integrity and safety of pipelines by filling them with water and pressurizing the system beyond normal operating levels. This test helps identify potential leaks, weak points, or construction flaws by sealing the pipeline, maintaining pressure for a specified period and monitoring for any pressure loss. Typically performed on new pipelines before they are commissioned, hydrostatic testing is also used to assess the condition of existing pipelines during routine maintenance or after repairs. The process is often mandated by regulatory bodies and industry standards to ensure compliance and safety. Requirements for testing vary depending on the type of pipeline—such as oil, gas, or water—and the regulations set by authorities like the U.S. Department of Transportation (DOT) or the Pipeline and Hazardous Materials Safety Administration (PHMSA).
The complexity of hydrostatic testing depends on factors like the size, length and location of the pipeline, as well as the specific conditions under which the test is conducted. Large or remote pipelines, for example, can pose challenges in terms of preparation, water sourcing and pressure management. Despite these challenges, hydrostatic testing remains a critical procedure for ensuring the long-term safety and reliability of pipeline infrastructure.
What is the Hydrostatic Testing Procedure?
To ensure that a pipeline can withstand its expected operating conditions, hydrostatic testing includes the following steps:
Preparation: The pipeline is inspected, cleaned, and sealed at both ends. Valves, meters, or other sensitive equipment may be isolated or removed to prevent damage.
Filling: The pipeline is filled with water, ensuring that all air is purged to avoid inaccurate pressure readings. In some cases, a corrosion inhibitor may be added to the water.
Pressurization: The water is pressurized using pumps to a level higher than the pipeline’s normal operating pressure, typically between 1.25 to 1.5 times the operating pressure.
Hold Period: The system is maintained at this elevated pressure for a specific duration, which can range from 30 minutes to several hours, depending on regulations and pipeline conditions.
Monitoring: Pressure and any potential leaks are carefully monitored during the test period. A drop in pressure may indicate a leak or weak spot.
Inspection and Analysis: If the pressure holds steady, the pipeline passes the test. If there are leaks, they are located, repaired and the test may be repeated.
Water Disposal: After the test, the water is carefully removed, treated, and disposed of according to environmental guidelines.
Certification and Documentation: A report is generated to document the test results, including pressure readings, duration and any corrective actions taken. This documentation is essential for regulatory compliance.
Evolution of Pipeline Hydrostatic Testing: Changing Complexity and New Requirements
Higher testing pressure and higher % SMYS (Specified Minimum Yield Strength) requirements were established in the 1960s. ASME B31.1.8 was the first standard to require post-construction testing. Modern pipeline pressure tests occur at high % SMYS levels and may utilize a “spike” test interval (short time duration) as an assessment of narrow, crack-like defects that may exist in the pipe.
While Maximum Operating Pressure (MOP) testing methods have not significantly changed over the past several decades, there have been a few newer applications that have been added to the testing methodology, such as “spike” testing at high % SMYS of the pipe. Detailed planning and thorough documentation will improve the probably of a successful outcome. In addition to all the planning, clear communication of expectations and testing requirements is essential for success throughout all phases of the planning and execution of the test.
Benefits of Third-Party Pipeline Hydrostatic Testing Services
Hydrostatic testing a pipeline is a necessary part of the commissioning process during new construction to verify structural integrity and to meet requirement for establishing a Maximum Operating Pressure. Pipeline hydrostatic tests can also re-certify the pipeline after a change in service or modification to the pipe. Hydrotests can be used as an alternative or enhancement to In-Line Inspection techniques, especially for crack-like defects.
Each hydrotest has unique challenges that need to be considered prior to executing the test. A few of the primary concerns include water fill without entraining air, temperature stabilization and accurate temperature measurement. Working with an expert testing partner saves time and money and ensures proper compliance and certification in support of a successful hydrostatic test.
Working with a third part testing partner is more efficient and cost effective when it comes to proper pipeline certification. To leverage the full benefits of third-party testing, seek a highly qualified and experienced team who understands the requirements and your goals.
Essential Hydrostatic Testing Equipment
Pipeline operators often do not own the specialized equipment required for hydrostatic testing, including high flow rate and high-pressure pumps that are used for the displacement of product with water. Many hydrostatic testing evolutions require additional experienced people and equipment for a successful test. A testing partner will have access to modern hydrostatic testing equipment that complies with the U.S. Department of Transportation (DOT) standards and should have experience with implementing testing processes in accordance with DOT requirements.
Accurate Hydrotest Data and Reliable Documentation
A successful hydrostatic test will produce the engineering data necessary for the MOP of the pipeline. Successfully completing the hydrostatic test and providing the necessary documentation is essential when the pipeline operations are audited by State or Federal officials. Without a properly conducted hydrostatic pipeline test and the documentation to justify the MOP of the pipeline, issues could become a regulator’s audit findings. A quality third-party testing partner understands the challenges related to poor documentation and incomplete test records. Managing this process from beginning to end with attention to detail and proper procedure, a third party increases the probability of a successful hydrostatic test.
Ensure Compliance and Certification in Pipeline Hydrostatic Testing
Certifying the results of hydrostatic testing requires support from a qualified individual or team of experts. Independent contractors can attest that the hydrostatic test was successfully executed and provide the required compliance and engineering documentation associated with the test. Repeating a hydrotest because of a planning mistake, failure in communication or an issue with the pipeline is often very expensive. Third party consultant involvement can reduce the risk of cost and execution inefficiency resulting in longer hydrostatic tests or having to shut a pipeline down again to repeat a test.
Cost Savings and Operational Efficiencies
A trusted third-party can help focus internal resources on the larger scope of executing the pipeline pressure test project successfully rather than be caught up in the details of properly executing the hydrostatic test. An experienced testing team will be able to make final determinations of a “good” test per ROPI calculations.
Third-party hydrostatic pipeline testers also help eliminate the qualification and training costs associated with tasking in-house staff with managing the hydrostatic test and associated recordkeeping. With an independent view of lessons learned and improvement opportunities, an outside testing group can help advance and achieve operational efficiencies for future testing.
Next Steps for Successful Pipeline Hydrostatic Testing: How TRC Can Help
Partnering with a third-party hydrostatic testing organization as early as the project planning phase is helpful. A qualified team will review your assets and test plan to ensure that the tests meet the appropriate standards and regulatory code requirements prior to the hydrostatic test execution. Having the testers onsite to examine the details of the test set-up, testing equipment and P-V plot preparation and to witness the test firsthand is essential. After the test has been completed, written documentation, forms and a report detailing all findings are provided.
As a trusted third-party pipeline hydrostatic tester, TRC’s engineers plan, design, QA/QC, witness and certify hydrostatic tests and provide the associated required documentation to support successful pipeline projects. Our pipeline experts work with your team to meet your specific testing challenges and to provide the best solutions to protect your assets.
We are also skilled in training pipeline operators in the skills necessary to successfully oversee hydrostatic testing, ensuring that your employees know what questions to ask and follow critical steps so that the test is appropriately executed.
For more information about our solutions or to discuss your unique project needs, contact Rodney Vasquez at rvasquez@trccompanies.com.